WELCOME TO PRINTED ARMIES
3D printed miniatures inspired by gaming pop culturePrinted Armies is creating 3D printed miniatures inspired by gaming pop culture. Helping you to build better miniature bases and vehicles. Crafted with a love for strategy gaming and science fiction.
If you want to stay up to date, see more or leave a comment, you can follow Printed Armies on Facebook and Instagram. And if you really like what you see and want to support this project, you can go to the Patreon page and get access to some exlusive goodies.
Should you have any questions, head down to the FAQ section or straight to the Contact form.
THE LORE
Latest IntelligenceThe year is 2060. A sudden shift in the magnetic field of the earth has caused an acceleration in the continental drift. Tsunamis, earthquakes and a dramatically increased volcanic activity all over the world have devastated the centers of population, leaving once flourishing cities and nations in ruins.
Toxic gases and dusts have forced the survivors to live in hermetically sealed habitats and to wear full-body protection when stepping out into the now hostile wasteland, scraping whatever they can find to survive in these harsh conditions.
The new environmental conditions forced the industries to abandon the established resource gathering technologies. Instead, volcanic pipes formed by the tectonic movements became the primary resource as mineral-rich igneous rocks and crystals form continuously at the surface from molten lava. Harvesting and processing those rocks and crystals provide the survivors with valuable raw materials for the industrial complexes.
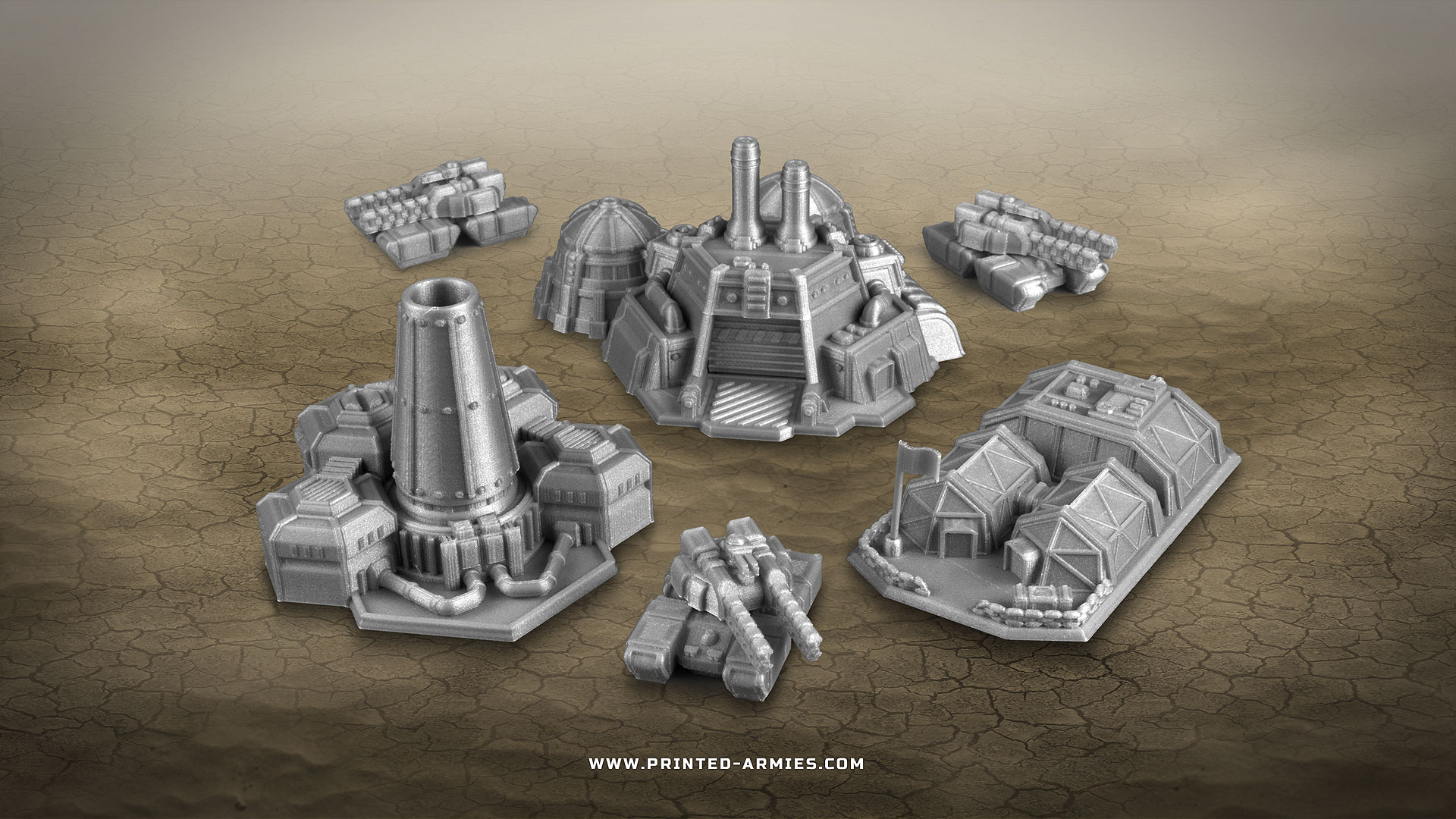
The political order shifted drastically. From the ashes of nations and the UN arose a world government, seeking to ensure the survival of the human race and granting stability to the survivors. Soon falling to the same fallacies as those, who came before them, bureaucracy and drowsiness once again slow down the actions so desperately needed.
A group of high-ranking scientists, world leading specialists in their fields, grew disillusioned enough to abandon the world government and seceded to a new organization built on the belief in scientific progress with all means necessary.
With both factions harboring diametrically opposed views on how to ensure humanity’s survival, it didn’t take long for the first violent conflicts to arise. Today the world is in a constant state of war, as both factions fight over what is left of the devestated planet.
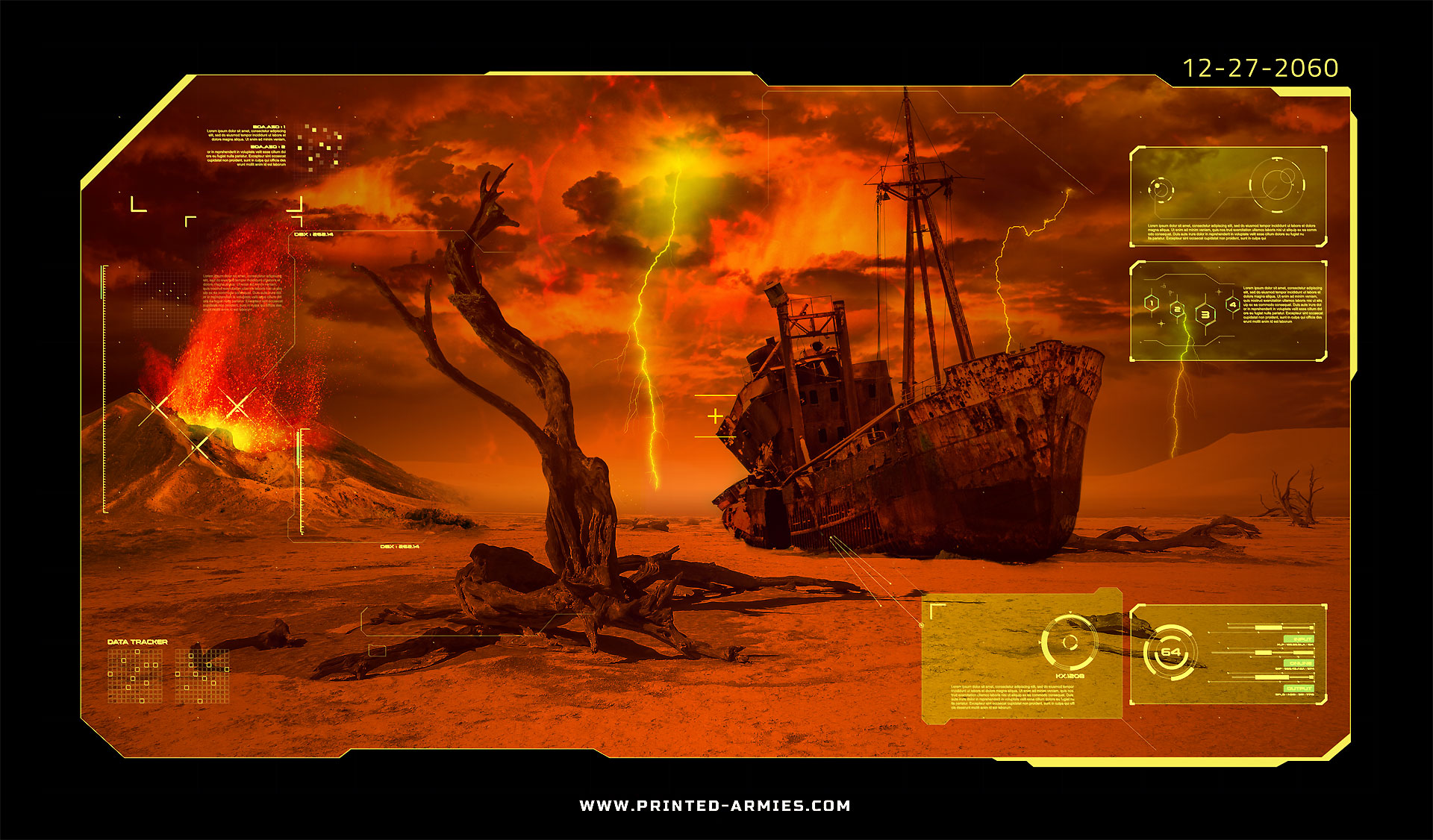
3D PRINTED MINIATURES
All prototypes printed on the Ultimaker 2+All miniatures below are available as digital 3D files on the Etsy shop. And if you don’t have access to a 3D printer yourself, you can get the physical printed miniatures over at the Shapeways shop. The 3D files can also be obtained as part of the „3D Model Flatrate“ by becoming a Patreon.
All miniatures are primarily designed to be 3D printed at a scale of 1:350, but can be upscaled for different gaming needs of course. I have also test printed some of the miniatures at a bigger scale of 1:200 and they still look great.
HOW TO GET THE MINIATURES
There are 3 options avilableDepending on you having access to a 3D printer yourself or not, there are 3 different options available. If you’re looking to get only the digital 3D files, you can obtain them either through direct purchase at the Etsy shop or by becoming a Patron of Printed Armies and pledging for the „3D Model Flatrate“.
If you don’t know anything about this whole 3D printing thing, you can still purchase the miniatures at the Shapeways shop. They do 3D printing on demand and are considered to be industry standard.
See the table below to get an overview about the pros and cons of each option.
BECOME A PATREON
Support Printed Armies and unlock exclusive goodiesIf you like my work and want to support this project, you can do so by becoming a Patreon of mine. The website Patreon.com is a membership platform, where you can donate in form of a monthly subscription. Depending on your pledge you unlock several exclusive goodies.
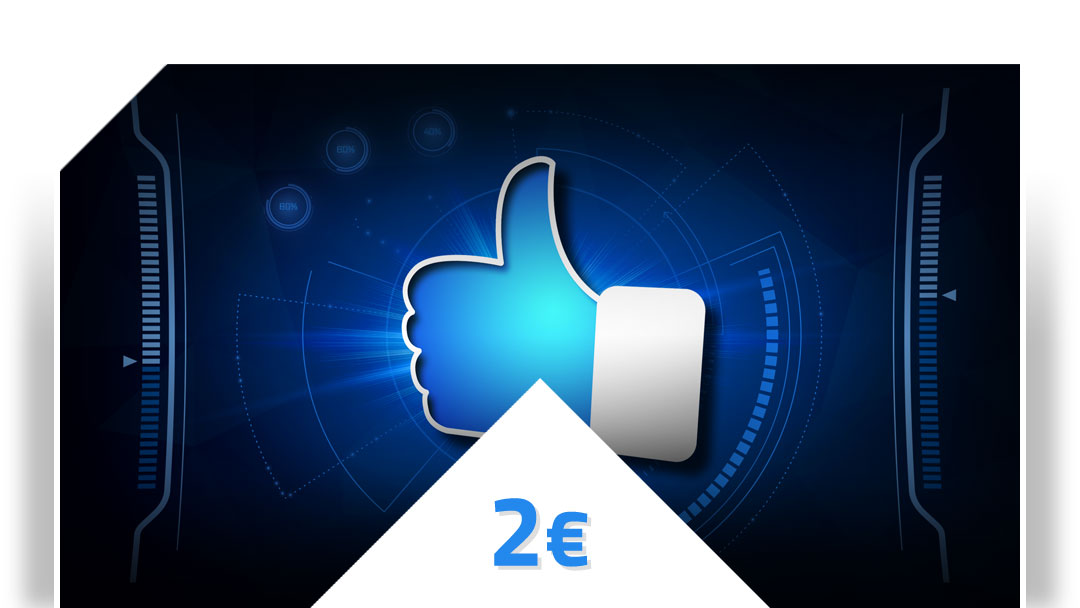
Thank you
If you don’t have much to spare and don’t expect anything in return, yet you still want to help supporting this project, this is the pledge for you.
So, thank you very much for your support. Every credit counts and helps to keep the production up and running.
Your help allows me to keep doing what I love.
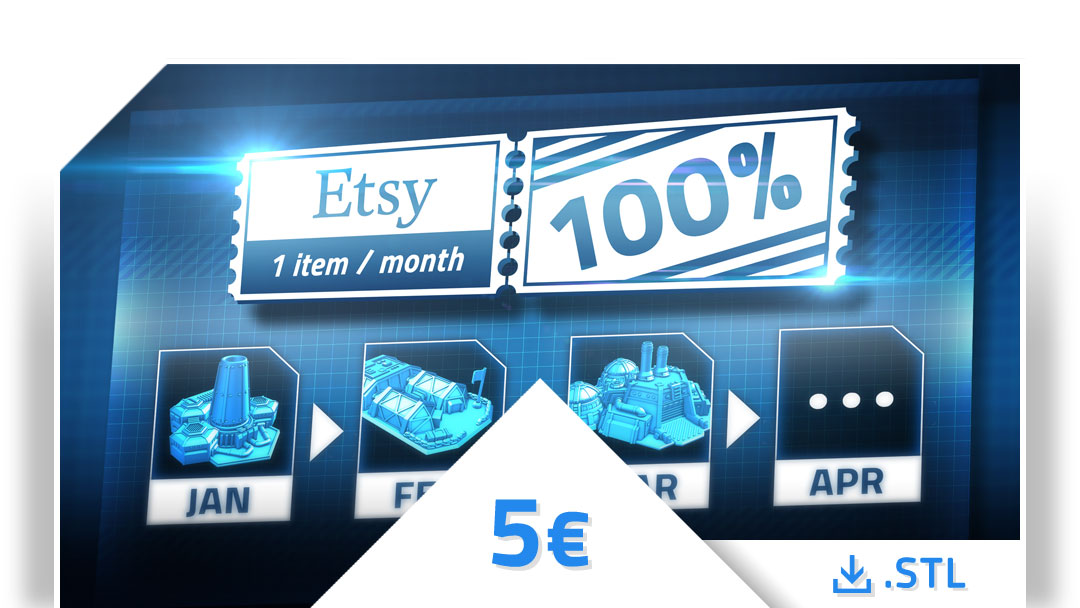
3D Model Flatrate
You get a coupon for the Etsy shop, granting you a 100% discount on a new 3D model .STL-file designed for 3D printing (suitable for FDM and SLA/DLP machines) every month.
This way you will save a lot of money in the long run, compared to getting the individual files at full price (supposed your are the patient type and don’t need everything at once).
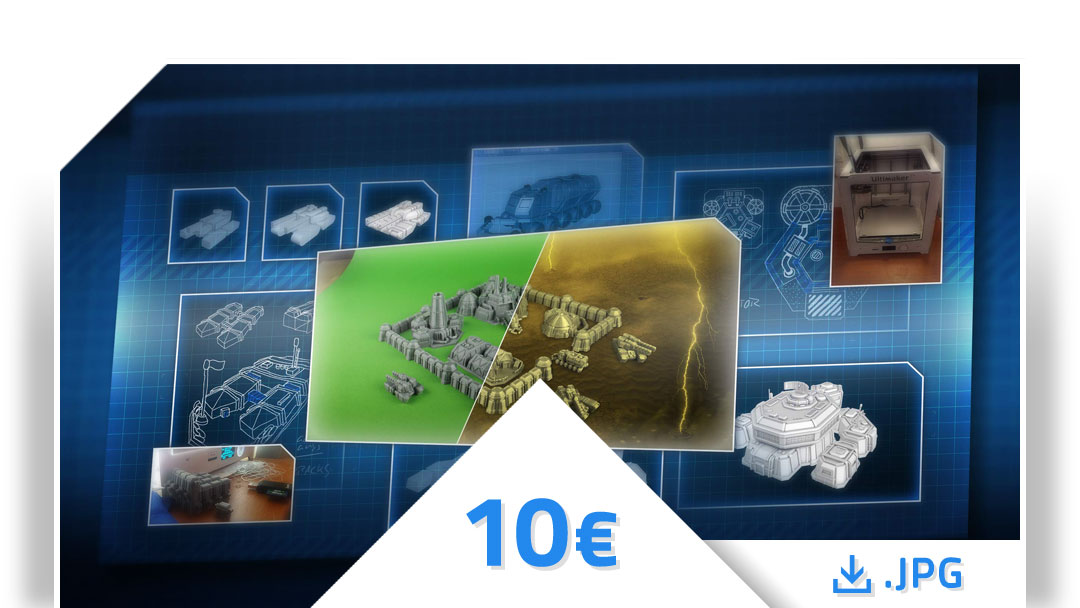
Behind the Scenes
For the fan, wo wants to catch a glimpse of the creative process behind my work.
You get download access to exclusive sketches, screenshots and photos, provided as digital JPG-files.
I will release new material multiple times per month.
Pledging for this tier grants you access to all previous lower tier rewards.
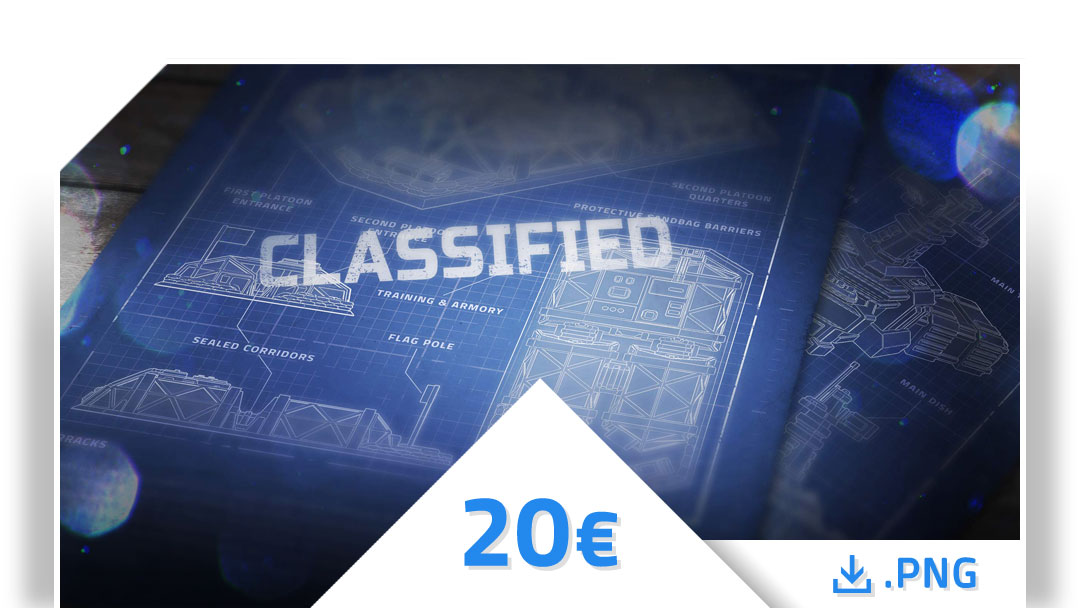
Blueprints
For the technical enthusiast.
You get download access to exclusive high resolution blue prints of all my finalized 3D miniatures, provided as digital PNG-files, printable at DIN A0 format (841 x 1189 cm).
I will release a new blue print poster every month.
Pledging for this tier grants you access to all previous lower tier rewards.
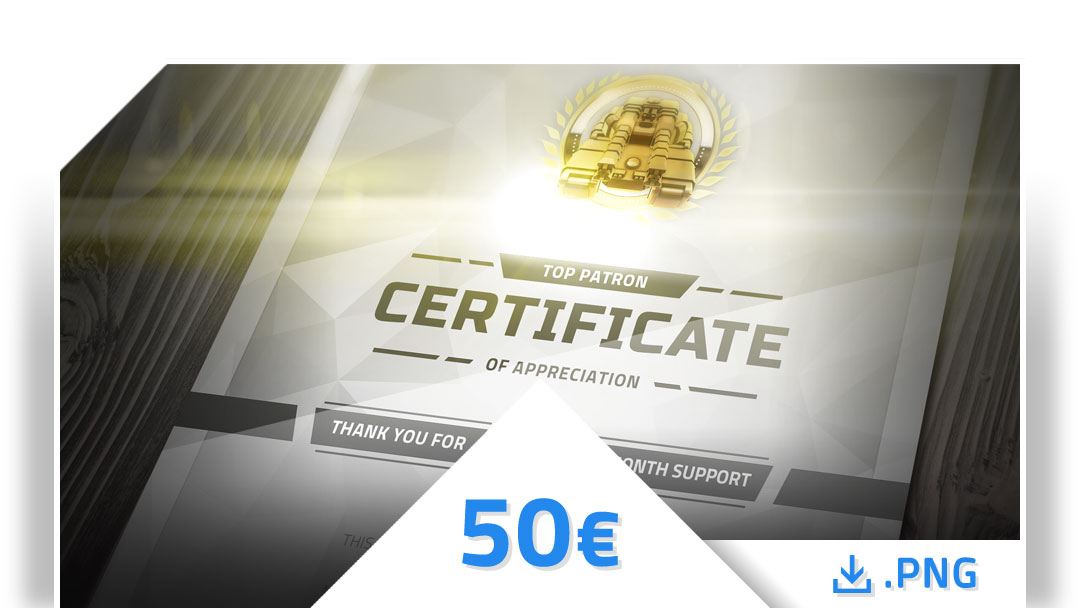
Personalized Top Patron Certificate
Only if you really don’t know where to put your money.
… and also if you consider yourself a die hard fan of Printed Armies and always wanted to hang and frame one (or multiple) certificates with your own name on it on the wall.
You will receive personalized upgraded certificates with new designs, titles and texts depending on the length of your continued support (after 1, 3, 6, 9 months, 1, 1 ½, 2, 2 ½ years etc.) as digital .PNG-files.
Pledging for this tier grants you access to all previous lower tier rewards.
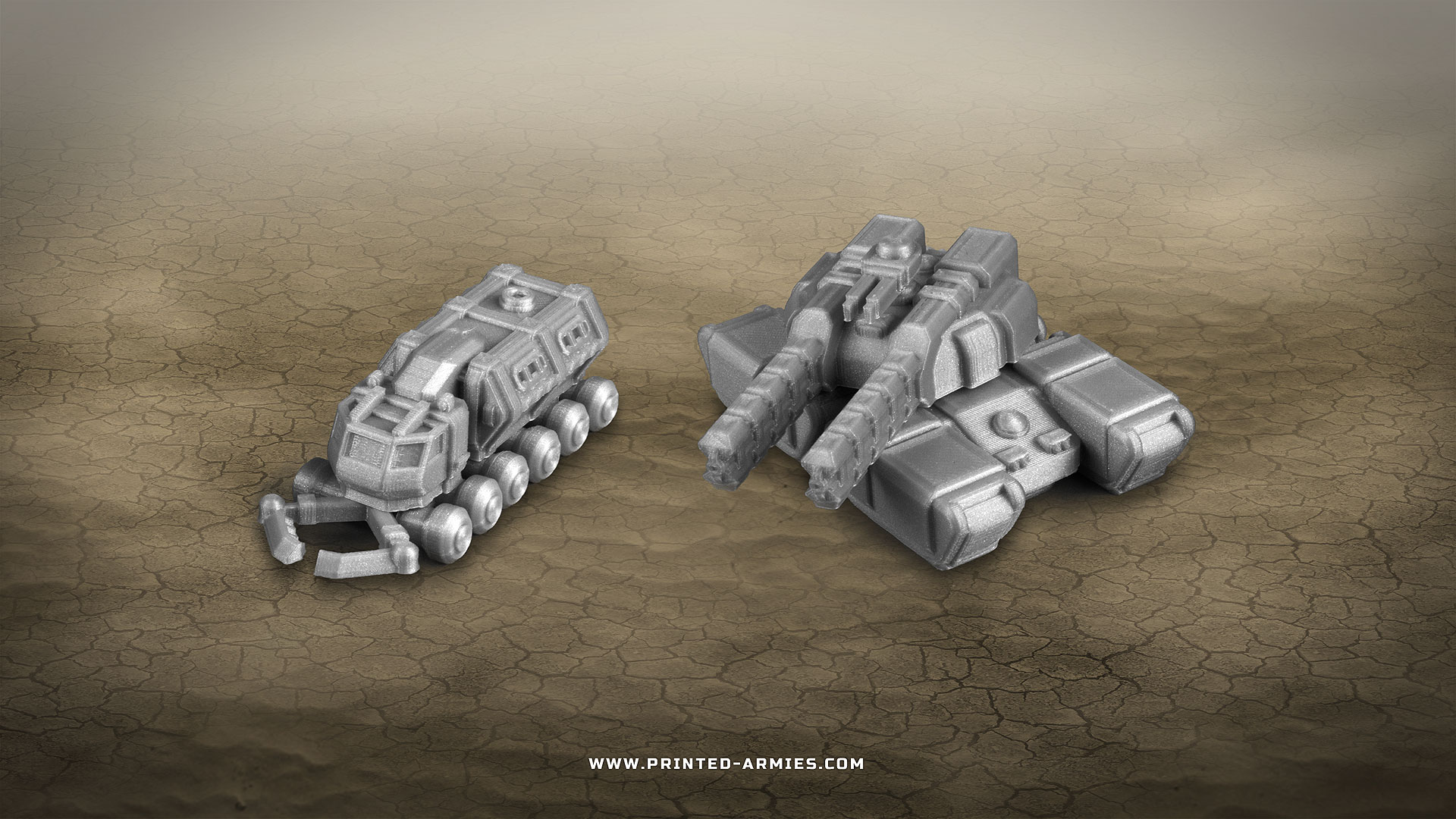
F.A.Q.
Freequently asked questionsI use the Ultimaker 2+. Yes, it was quite expensive, but it’s working flawless since I got it in 2016. So I can totally recommend it.
I use Cura. It’s free, it’s good, it has come a long way. I can recommend it.
I use Ultimaker Silver metallic PLA. I really like the shiny finish, that lets the miniatures look good even when they’re not painted.
Filament is the thin plastic, coiled up to a spool, that feeds the 3D printer. It gets attached of the backside of the machine and feeds into the printer by a set of small gears. It gets transported to the nozzle where it gets molten, so the printer can write with it like a mechanic pen.
I use Cinema 4D. Since I touched the program during my studies and also since I am a motion graphics designer by profession, it was the logical choice for me to use it also for creating my miniatures. But there are certainly cheaper alternatives out there, that you can use, like Blender or Fusion 360.
Here are some of the settings that I use and also recommend when printing my miniatures:
QUALITY
Layer Height: 0.1 mm
Initial Layer Height: 0.26 mm
Line Width: 0.4 mm
Initial Layer Line Width: 100 %
SHELL
Wall Thickness: 1.2 mm
Wall Line Count: 3
Top Thickness: 0.8 mm
Bottom Thickness: 0.8 mm
Top Layers: 8
Bottom Layers: 8
INFILL
Infill Density: 15 %
SPEED
Print Speed: 30 mm/s
Infill Speed: 30 mm/s
Wall Speed: 24 mm/s
Outer Wall Speed: 30 mm/s
Inner Wall Speed: 40 mm/s
Top/Bottom Speed: 20 mm/s
Travel Speed: 120 mm/s
Initial Layer Speed: 18 mm/s
Skirt/Brim Speed: 18 mm/s
I have a so called ReMarkable graphic tablet. It’s awesome, I love it.
First I make some sketches on my ReMarkable graphic tablet. Then I switch over to the PC to boot up Cinema 4D for the modeling part. I start with the rough shapes, and once everything feels right, I add the details. After that I export the 3D model as a .STL file and load it with Cura for the pre-visualisation. There I usually discover a few things that need changes to print properly. So I had back to Cinema for adjustments, rinse and repeat. When I can’t make out any more flaws, it’s time for a test print. And if that turns out fine, the model is done. If you want to catch a glimpse of that whole process, there’s a „Behind the Scenes“ tier over at Patreon.
I play mostly Command & Conquer (in fact I am a huge fan), but I also really enjoy Cities Skylines, Anno 1404, Dungeon Keeper or Desperados 3. I also recently discovered some small relaxing strategy building games like Islanders, Dorfromantik and Townscaper.
Yes, of course. You simply set the scaling with the slicer software of your choice.
My miniatures are primarily designed to be printed at a scale of 1:350. If you want to go bigger to let’s say 1:72, the calculation goes like this: „Smaller scale“ devided by „bigger scale“ equals the „factor“ that you need to enter at your slicer for upscaling. In our example it would be „350 : 72 = 4,861“. That means, when 100% size equals the original 1:350 scale, then you need to tell the slicer to print the miniature at 486,1% to get to the desired scale of 1:72.
There are multiple reasons for choosing that rather small scale. For once smaller prints reduce the printing time, enabling me to do faster iterations on the models. Moreover smaller prints require less space, which is good for people with smaller printers. The miniatures also take up less space when you display them at your desk that way. Only being able to put 2 or 3 buildingsnext to each other before running out of space is only half the fun when wanting to construct a huge base. And last but not least I find the size actually pretty fitting as it just feels like playing a stretegy game and looking down on your base from a bird’s eye perspective.
Yes, I do. I will make bigger versions of all the vehicles with more details especially designed for that purpose. I will also look into cutting the buildings into smaller pieces, so that they can be printed at the scale used for tabletop/wargaming.
That depends on the size of the model. Smaller ones take less time, larger ones take more time. I keep that in mind when designing the miniatures. So I end up with something in between half an hour and up to 10 or 12 hours of printing time per model.
Because I’m just not good at it! No, jokes aside, I always felt more comfortable with a pen or pencil (and later with a mouse and keyboard) compared to using a brush. I know, it’s all a matter of „practice makes perfect“ and I already got a set of colors, brushes, even an airbrush and a compressor, but I just can’t find the time to practice properly. I hope that changes at some point in the future though.
That’s simply because I couldn’t deliver on that kind of mass production with currently only one 3D printer. Let’s assume somebody orders a set of 10 different buildings, that would take me already around one week of printing for only that one order. Now think about having multiple orders at once. And during that time I can’t test print new prototypes. So in short it’s just more practical if Shapeways handles that part for me.
After downloading the files you are allowed to print as many physical miniatures as you like and give these miniatures to up to 5 people such as your close friends and relatives. Exceeding this number is forbidden. I am thinking about adding a dedicated „Reseller“ tier to the Patreon campaign, which will grant you the right to sell / redistribute the printed (and possibly painted) miniatures (not the files) if there should be a demand for that.
CONTACT
How to reach meIf you have any further questions, feel free to contact me. Just drop me an e-mail by using the address below or simply use the contact from. You can also reach out to me through my social media channels. I’m always happy to get in touch with my little community and talk about games, 3D printing and all kinds of stuff.
If I shouldn’t answer your e-mail in a timely manner, just ping me on Facebook or Instagram, as they sometimes end up in the spam folder.